ErtelAlsop offers many different grades of Diatomaceous Earth (DE) to accommodate our customers with their clarification needs. Whether you need a bag or a pallet, ErtelAlsop can supply you with Standard DE, HyFlo DE, or ultra pure, acid washed Celpure. For more information please see below, or contact ErtelAlsop for more information.
Celpure
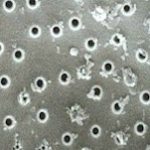
Scanning electron micrograph of conventional food grade diatom surface (5000x). Conventional diatomite undergoes calcination without purification, this fuses impurities to the diatoms surface.
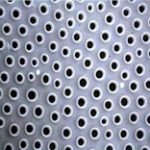
Scanning electron micrograph of Celpure diatom surface (5000x). Celpure media undergoes calcination after purification. This minimizes impurities and increases bulk density.
ErtelAlsop carries the following grades of Celpure Diatomaceous Earth:
Celpure® is a highly purified diatomaceous earth for use in the maintenance of filter cake permeability through the bodyfeed of the media upstream of the filter press, filter housing or vessel. Due to the exceptional high purity of this filter aid, Celpure® diatomite is particularly well suited for pressure filtration in high purity chemical, food & beverage, and critical pharmaceutical or biotech applications.
Celpure patented manufacturing process is a major advance in filter aid technology and produced in a standalone FDA approved facility. The process generates a media that surpasses conventional diatomite filter aids in purity, performance, regulatory support, and finished product consistency.
Studies and field experience show that after replacing conventional diatomite filter aids with Celpure diatomite filter aids, extractable impurities are significantly reduced adding to more consistent processes and improved yields.
Celpure® filter aid production is structured to meet the requirements of ISO9002 as well as the appropriate CGMPs and guidance documents.
Comparing Conventional Diatomite vs. Celpure Filter Aids
Celite
ErtelAlsop carries the following grades of Celite Diatomaceous Earth:
Hyflo Super-Cel_Technical Data
CELITE Diatomaceous Earth has a more intricate particle shape than standard Diatomaceous Earth, and thus provides a more tortuous path for suspended particles to be trapped.
How to Use diatomaceous earth as a filter aid
Continuous addition of Diatomaceous Earth filter aid (body feeding) is accomplished either by feeding filter aid in a slurry or by dry feeding. Slurry feeding is usually done with plunger or diaphragm pumps. If filtration is a batch process, the filter aid can be added directly to the batch.
In the operation of a filtration system, the filter is first precoated by circulating a mixture of Diatomaceous Earth and clear or filtered liquid from the precoat tank through the filter and back to the precoat tank. This is continued until all the filter aid is deposited on the filter media or screen. The body feed injection system is then started and the filter is changed over, with minimum fluctuations in pressure, from precoating to filtering.
PRECOATING
The first step in the use of Diatomaceous Earth is to build up a “precoat” of filter aid on the filter septum. The purpose of the precoat is threefold:
1. To prevent the filter septum from becoming clogged by impurities, thus prolonging septum life.
2. To give immediate clarity.
3. To facilitate cleaning of the septum at the end of the cycle.
Precoating is accomplished by circulating a slurry of Diatomaceous Earth and filtered or clear liquid between the filter and the precoat tank. Since most of the Diatomaceous Earth particles are smaller than the openings in the septum, they must form the precoat by bridging these openings. These bridges can be upset by air bubbles, sudden changes in pressure, or vibrations, causing the filtrate to become turbid until the upsetting influences have been corrected. If flow distribution in the filter is good, the filter may be filled with clear precoat liquid and a concentrated slurry of filter aid may then be pumped or educted into the filter followed by recirculation.
AMOUNT OF PRECOAT
The amount of precoat should be from 10 to 20 lbs of Diatomaceous Earth filter aid per 100sq. ft. of filter area. The greater amount being used when distribution of flow in the filter is poor, or in starting up new filters. If it is perfectly distributed, 10 lbs. (4.5 kg) of filter aid per 100 sq. ft. (9.29 sq. m) of filter area will give a precoat of approximately 1/16″ (1.6 mm) in thickness. Precoat slurry concentration will depend primarily on the ratio of filter area to the liquid volume of the filter and piping. If the concentration is much below 0.3%, precoating may be difficult since the formation of the bridge depends partly on the “crowding” effect of the particles of DE trying to get through the septum openings.
PRECOATING RATE
The precoat pumping rate will depend mainly on the viscosity of the liquid used. The rate should be sufficient to keep all the filter aid in suspension, but should not be fast enough to cause erosion of precoat in the filter. For water, a typical rate is from 1 to 2 gals. per sq. ft. of filter area per minute (gsfm). For viscous liquids, the rate may be as low as 5 gals. per sq. ft. per hour (gsfh). A general rule for precoating is to precoat at that rate which gives a differential pressure of approximately 2 lbs./sq. in (13.8 kilopascals). For water, an upward velocity of at least 4 1/2 ft./min. is required for proper filter aid suspension. The suspension of filter aid can be improved in the tank type, or pressure leaf filter, by recirculating part of the inlet flow from the top of the filter back to the precoat tank.
TROUBLESHOOTING
Precoating filtrate should clear up in 2 to 5 minutes. However, this does not mean the precoat is all in place. Continue precoating until the liquid in the filter shell is relatively clear. This usually takes place in 10 to 15 minutes at most. Lack of clarity of filtrate could be caused by any precoat erosion caused by too high a circulation rate; blinding of filter septum; insufficient precoat at top of leaves caused by too little circulation; tears in septum; old screens with worn and/or separated wires; leaks between septum and rum of leaf; worn gaskets between leaf discharge nipple and discharge manifold; wrinkles in septum; negative pressure on discharge manifold causing flashing inside the leaf.
Learn More About Pre-Coat & Body Feed